gtgt_bangbang
New member
Cutting the bracket shorter ; I used a die grinder w/ abrasive cut-off wheel.
Band clamp the die grinder to s/thing (securely ! this is the cut off length, dont want it to move half way around !)
The blade should overhanging shelf edge by length you want to cut off Head Light bracket HLB
This wire shelf is ideal; easy to clamp grinder to, nice slippery & square shelf face to steady the HLB against while rotating at blade.
The 2nd band clamp loosely slips over/off the grinders trigger to run free hand.
Fire up the grinder, focussing on holding top edge of HLB squarely against the shelf edge & rotate HLB against blade.
I cut ~1/3 around the bracket, then "rotate workpiece backward" and start a 2nd cut , traveling in the direction toward 1st kerf.
Stop this 2nd cut just slightly BEFORE reaching the 1st cut, to leave a little bridge between the keeper workpiece & the cutoff ring
I did 4 cuts like this, 4 bridges.
Leaving short bridges between cuts makes it TON UP easier to hold the work piece square & at intended distance, to get the best cut.
IF you just work in a straight line around, the HLB will eventually collapse toward cut off ring, snag the disc, fling HLB like poo, and all bets are off for how pretty the results. The goal is cut off accuratly and no deformation of course
When Bracket will be about 90% sliced, then nick through the bridges to free the ring.
I left the HL bracket a few MM long, because there is a Slacker Way of trimming to length in next post
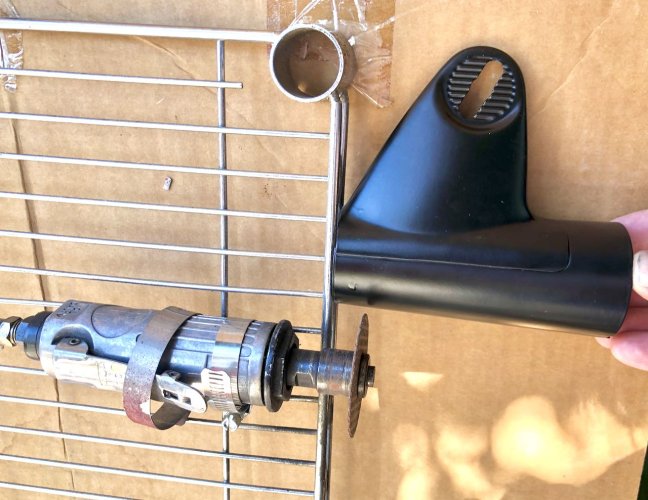
Band clamp the die grinder to s/thing (securely ! this is the cut off length, dont want it to move half way around !)
The blade should overhanging shelf edge by length you want to cut off Head Light bracket HLB
This wire shelf is ideal; easy to clamp grinder to, nice slippery & square shelf face to steady the HLB against while rotating at blade.
The 2nd band clamp loosely slips over/off the grinders trigger to run free hand.
Fire up the grinder, focussing on holding top edge of HLB squarely against the shelf edge & rotate HLB against blade.
I cut ~1/3 around the bracket, then "rotate workpiece backward" and start a 2nd cut , traveling in the direction toward 1st kerf.
Stop this 2nd cut just slightly BEFORE reaching the 1st cut, to leave a little bridge between the keeper workpiece & the cutoff ring
I did 4 cuts like this, 4 bridges.
Leaving short bridges between cuts makes it TON UP easier to hold the work piece square & at intended distance, to get the best cut.
IF you just work in a straight line around, the HLB will eventually collapse toward cut off ring, snag the disc, fling HLB like poo, and all bets are off for how pretty the results. The goal is cut off accuratly and no deformation of course
When Bracket will be about 90% sliced, then nick through the bridges to free the ring.
I left the HL bracket a few MM long, because there is a Slacker Way of trimming to length in next post
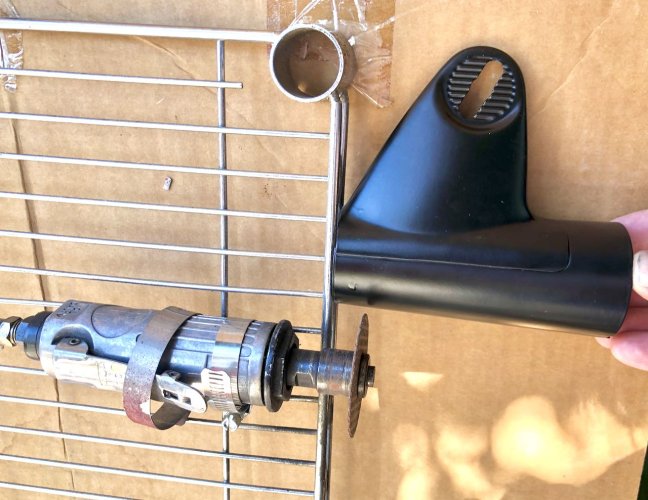
Last edited: