brook.reams
B Reams
1975 R75/6 Refresh Project
This bike, a 1975 R75/6, is the first BMW I bought and now has almost 106,000 miles on it.
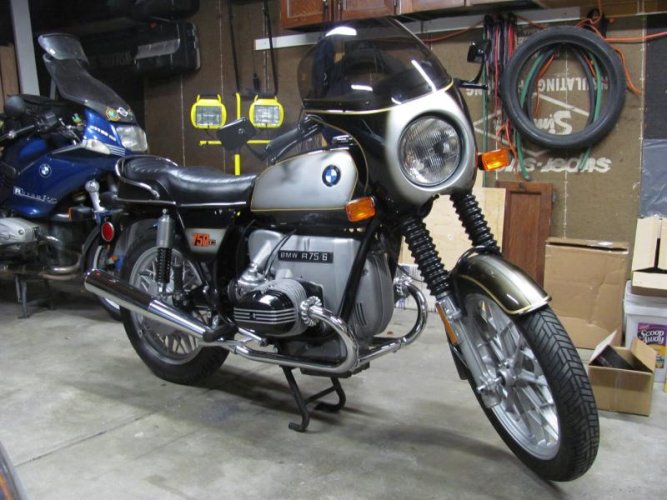
It is the first bike I rode more than 1,000 miles in one day back in 1976 and is the first build project I completed in 2010 and documented here:
I have several projects that I didn't get to during the build. One of these is replacing the timing chain which I document in the link below with a lot of pictures and detailed step-by-step procedure.
My bike has the duplex, dual row chain, while starting with the /7 series, the timing chain is a single row chain. This procedure should help you replace a /5, /6 or /7 series timing chain, but some of the parts will be different as I note in the write-up.
Since I stripped the bike I have the engine out of the frame, but most people will do this work with the engine in the frame. Although it is an option to remove the front wheel and forks to have clear access to the front of the engine, I think the work can be done without removing them.
Before starting this project, I reviewed material available on the Airheads Beemer Club site, www.airheads.org: I believe you can access the links in the write-up even if you are not a member, but consider joining this group if you want to contribute to the Airhead culture. I read material on Bob Fleischer's blog site, and I posted a number of questions to the Micapeak Airheads forum whose members are legend for providing thoughtful advice and encouragement. You should add these resources to your toolkit as they are authoritative with valuable information.
In particular, I want to acknowledge Ron Cichowski, Tom Cutter, Bob Fleischer, Doran Shields, Marten Walkker and Eric Zwicky on the Micapeak Airheads forum for answering my questions. Also, a local Colorado Airhead, Don Wreyford, came by to kibitz and help with the disassembly process. Don has always been generous with his time and knowledge. And, my youngest son, Branden, shown in many of the photos with the electric yellow shirt, helped me on the entire project with wrenching, picture taking, and good ideas and advice when we needed to stop and reconsider what we should do next. He is turning into an accomplished Airhead wrench and lover of Bavarian iron.
Here a couple of the pictures included in the detailed write-up you can access from the link above.
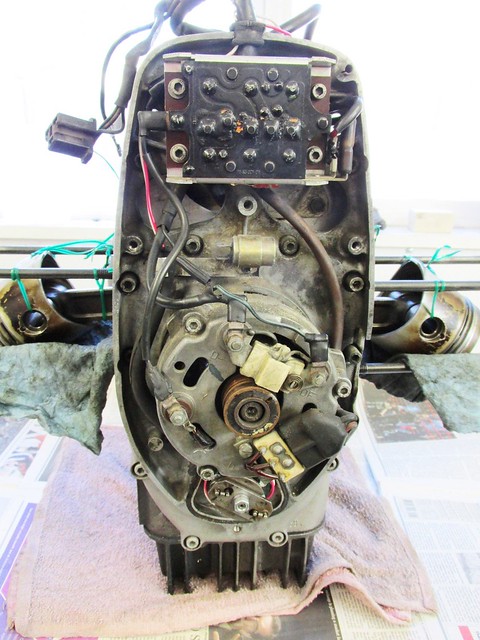
Ready To Start - Timing Cover Removed by Brook Reams, on Flickr
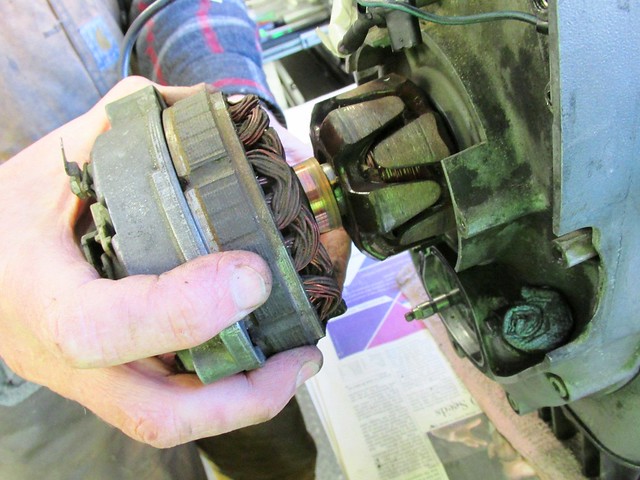
Alternator Stator and Housing Removed by Brook Reams, on Flickr
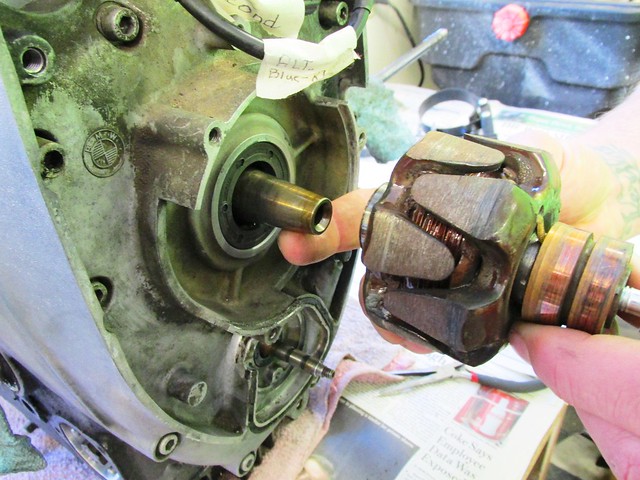
Alternator Rotor Fits on Taper of Crankshaft Nose by Brook Reams, on Flickr

Engine Electrics Harness with Labels by Brook Reams, on Flickr

Finger Tight and Cover Came Loose by Brook Reams, on Flickr
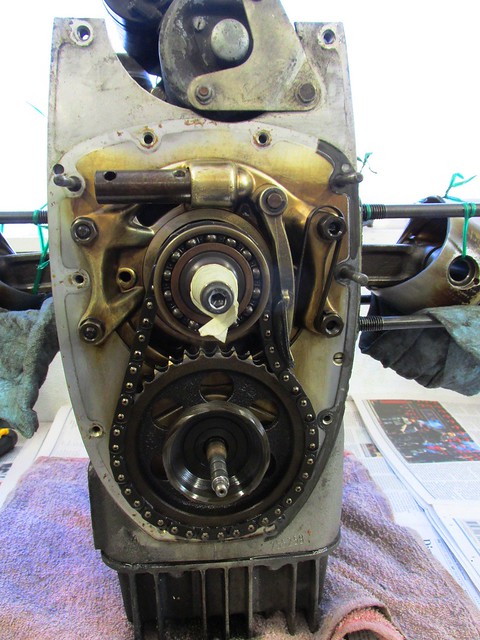
What's Under the Timing Cover by Brook Reams, on Flickr
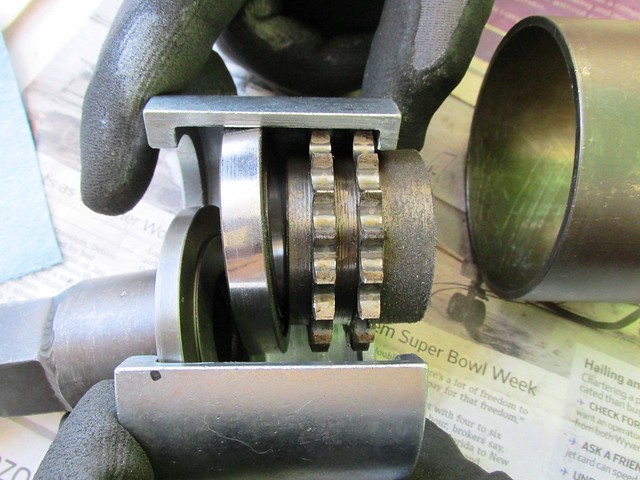
Crankshaft Nose Bearing and Sprocket in Cycle Works Removal Tool by Brook Reams, on Flickr
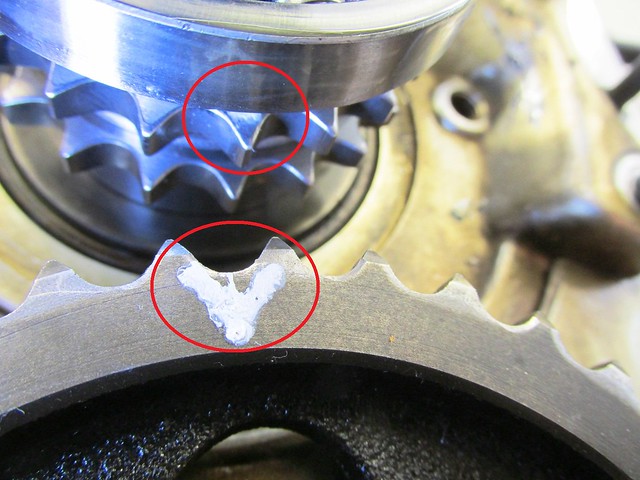
Crankshaft Sprocket and Camshaft Sprocket Timing Marks Aligned at TDC by Brook Reams, on Flickr
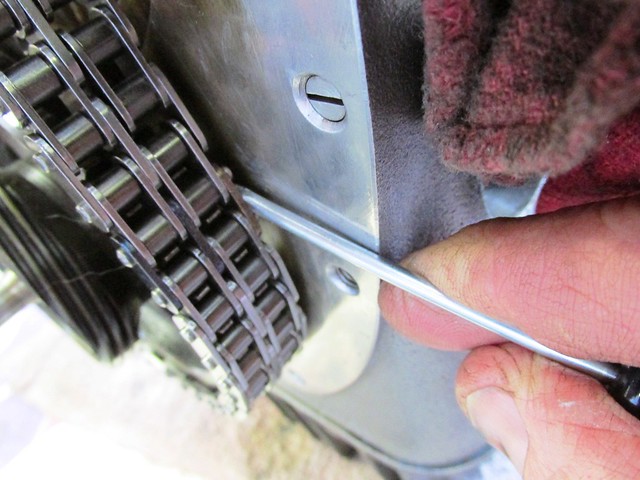
Installing Bronze Color Back Plate With Screw Driver Blade by Brook Reams, on Flickr
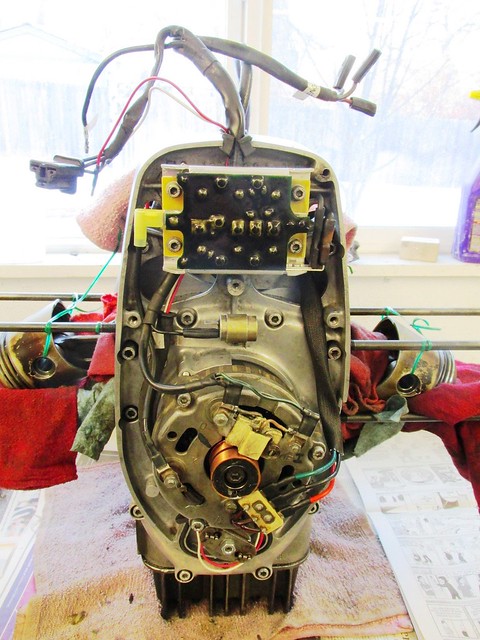
Finshed Engine Electrics Install by Brook Reams, on Flickr
This bike, a 1975 R75/6, is the first BMW I bought and now has almost 106,000 miles on it.
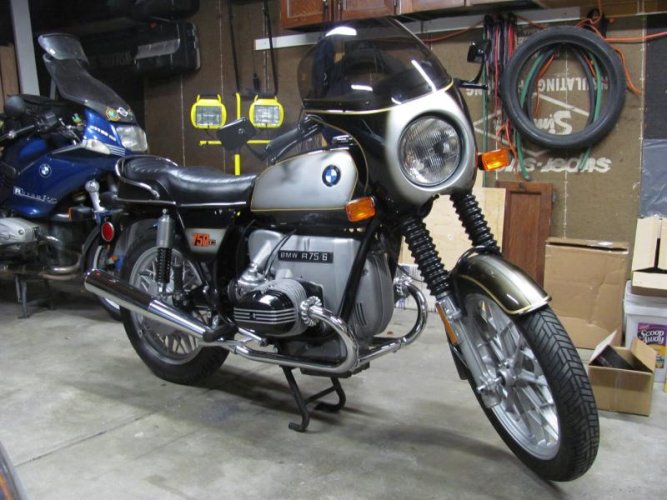
It is the first bike I rode more than 1,000 miles in one day back in 1976 and is the first build project I completed in 2010 and documented here:
I have several projects that I didn't get to during the build. One of these is replacing the timing chain which I document in the link below with a lot of pictures and detailed step-by-step procedure.
My bike has the duplex, dual row chain, while starting with the /7 series, the timing chain is a single row chain. This procedure should help you replace a /5, /6 or /7 series timing chain, but some of the parts will be different as I note in the write-up.
Since I stripped the bike I have the engine out of the frame, but most people will do this work with the engine in the frame. Although it is an option to remove the front wheel and forks to have clear access to the front of the engine, I think the work can be done without removing them.
Before starting this project, I reviewed material available on the Airheads Beemer Club site, www.airheads.org: I believe you can access the links in the write-up even if you are not a member, but consider joining this group if you want to contribute to the Airhead culture. I read material on Bob Fleischer's blog site, and I posted a number of questions to the Micapeak Airheads forum whose members are legend for providing thoughtful advice and encouragement. You should add these resources to your toolkit as they are authoritative with valuable information.
In particular, I want to acknowledge Ron Cichowski, Tom Cutter, Bob Fleischer, Doran Shields, Marten Walkker and Eric Zwicky on the Micapeak Airheads forum for answering my questions. Also, a local Colorado Airhead, Don Wreyford, came by to kibitz and help with the disassembly process. Don has always been generous with his time and knowledge. And, my youngest son, Branden, shown in many of the photos with the electric yellow shirt, helped me on the entire project with wrenching, picture taking, and good ideas and advice when we needed to stop and reconsider what we should do next. He is turning into an accomplished Airhead wrench and lover of Bavarian iron.
Here a couple of the pictures included in the detailed write-up you can access from the link above.
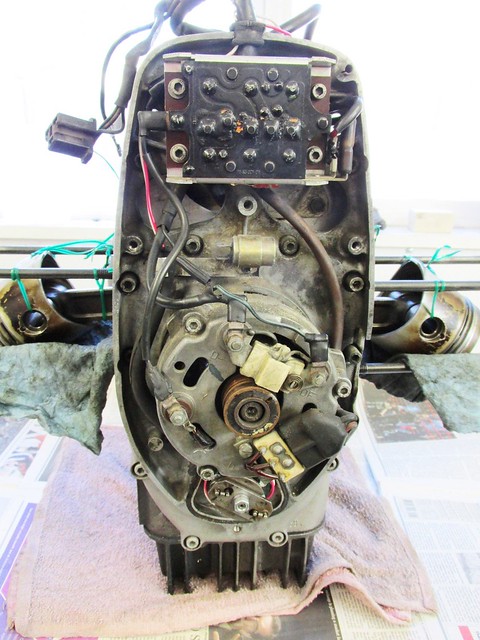
Ready To Start - Timing Cover Removed by Brook Reams, on Flickr
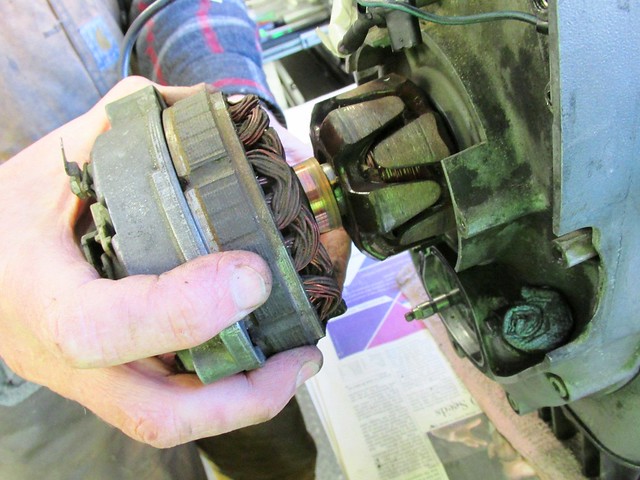
Alternator Stator and Housing Removed by Brook Reams, on Flickr
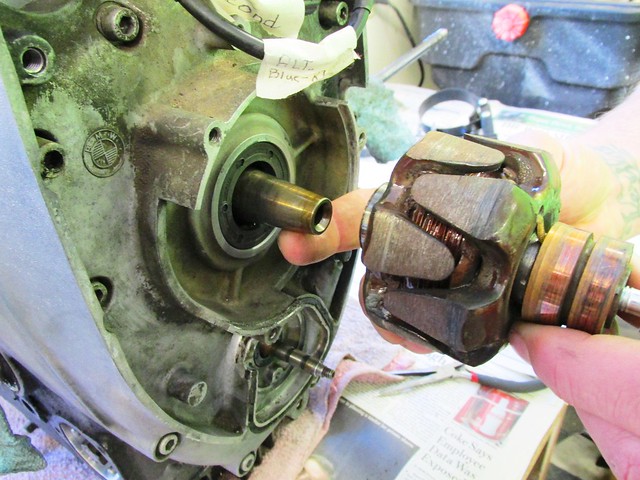
Alternator Rotor Fits on Taper of Crankshaft Nose by Brook Reams, on Flickr

Engine Electrics Harness with Labels by Brook Reams, on Flickr

Finger Tight and Cover Came Loose by Brook Reams, on Flickr
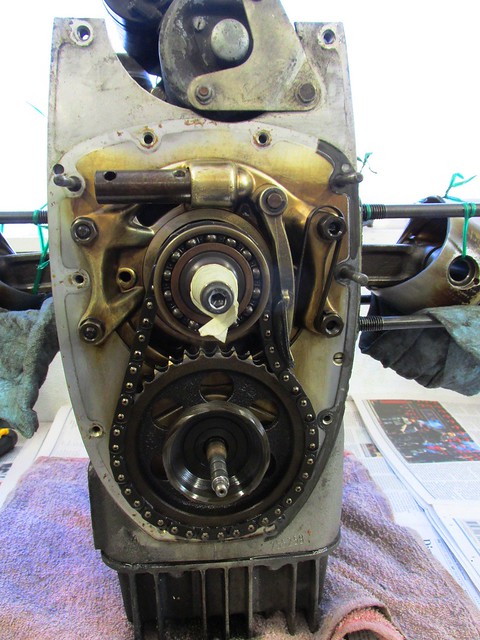
What's Under the Timing Cover by Brook Reams, on Flickr
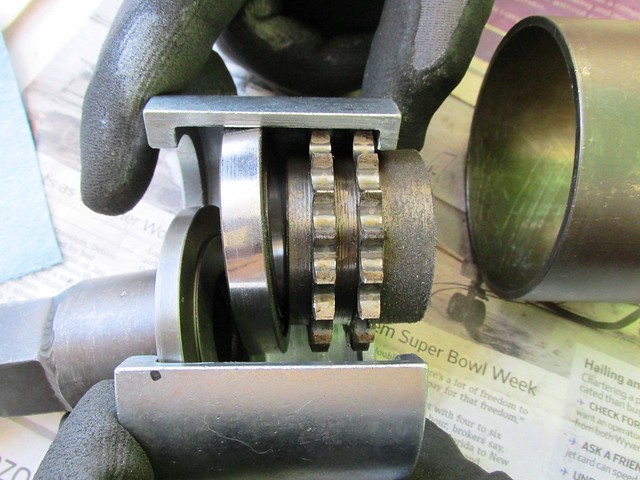
Crankshaft Nose Bearing and Sprocket in Cycle Works Removal Tool by Brook Reams, on Flickr
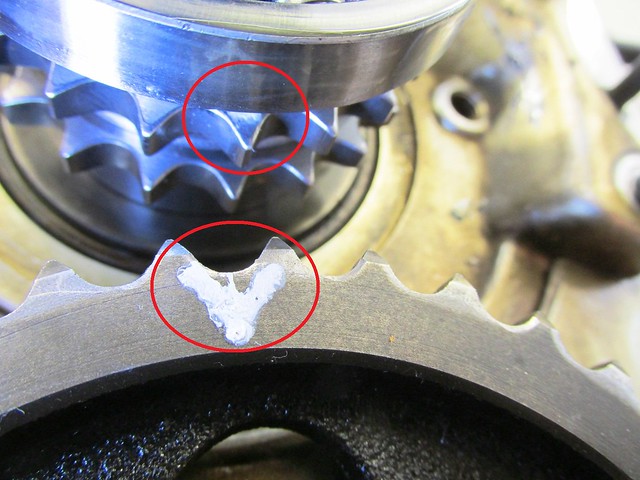
Crankshaft Sprocket and Camshaft Sprocket Timing Marks Aligned at TDC by Brook Reams, on Flickr
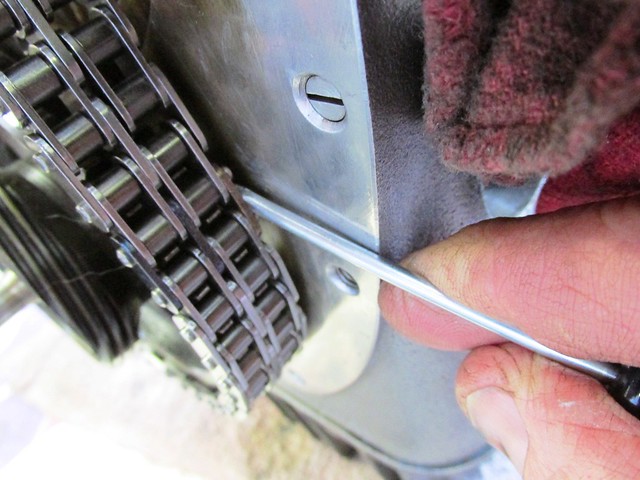
Installing Bronze Color Back Plate With Screw Driver Blade by Brook Reams, on Flickr
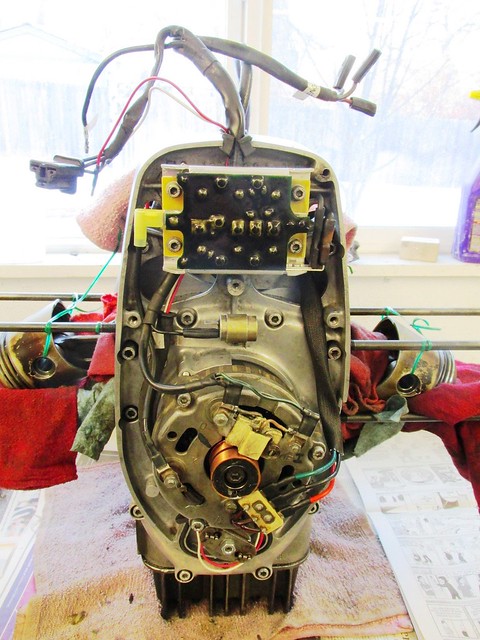
Finshed Engine Electrics Install by Brook Reams, on Flickr
Last edited: