sundance71
New member
Hi folks.
I'm getting ready to change out the clutch on my 04 R1150Rt with the longer splined hub. I went ahead and got the pressure plate and clutch cover as well from Beemer Boneyard. The parts came in today and look good but I was wondering about one thing.
In all of the photos and videos that I've seen, the cover and pressure plate are balanced by drilling indents in specific locations on the part.
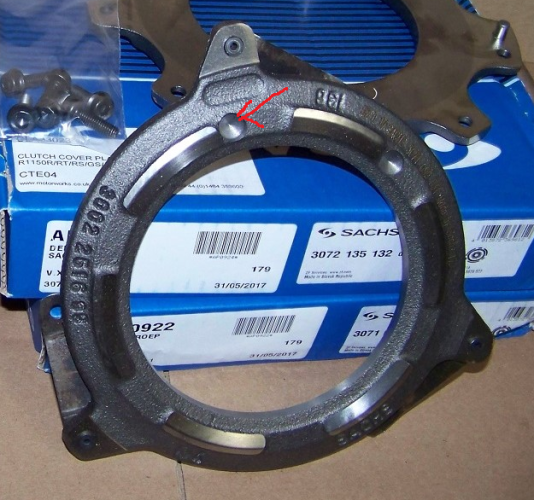
The parts that I received don't look like any material was removed from anywhere. How can they be balanced unless I just lucked out and got two perfect parts? I may be overthinking this but getting to the clutch is a major PITA and I don't want to get everything back together and have vibration issues. Does anyone else have any experience with this?
Thanks
Chris
I'm getting ready to change out the clutch on my 04 R1150Rt with the longer splined hub. I went ahead and got the pressure plate and clutch cover as well from Beemer Boneyard. The parts came in today and look good but I was wondering about one thing.
In all of the photos and videos that I've seen, the cover and pressure plate are balanced by drilling indents in specific locations on the part.
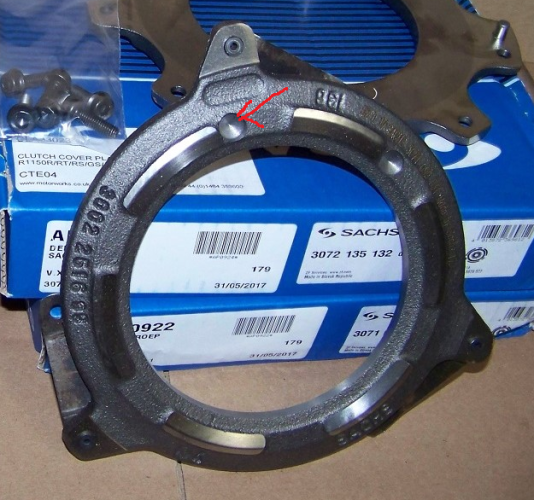
The parts that I received don't look like any material was removed from anywhere. How can they be balanced unless I just lucked out and got two perfect parts? I may be overthinking this but getting to the clutch is a major PITA and I don't want to get everything back together and have vibration issues. Does anyone else have any experience with this?
Thanks
Chris